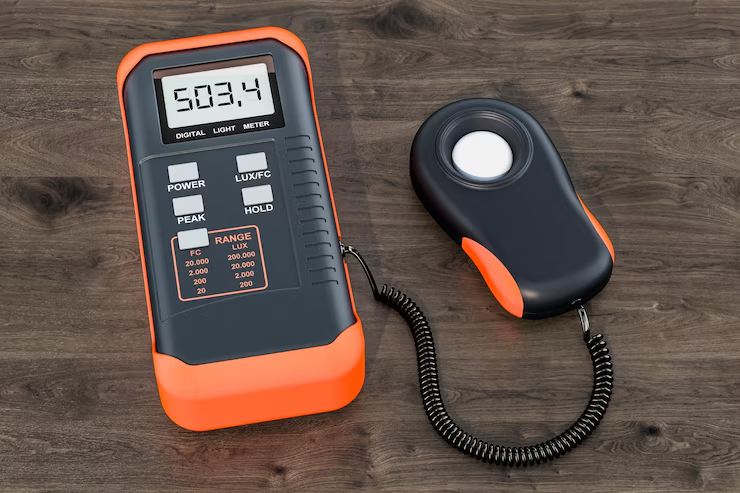
Table of Contents
Introduction
What is an NDT Ultrasonic Thickness Gauge?
Key Applications of NDT Ultrasonic Thickness Gauges
Benefits of Using an Ultrasonic Thickness Gauge
When to Use an Ultrasonic Thickness Gauge
Conclusion
Introduction
In industries where safety, quality, and durability are non-negotiable, ensuring the structural integrity of materials is crucial. That’s where an NDT Ultrasonic Thickness Gauge becomes an essential tool. Whether you’re working in oil and gas, shipbuilding, power generation, aerospace, or manufacturing, understanding the exact thickness of a component without damaging it can save time, money, and—most importantly—lives.
NDT (Non-Destructive Testing) using ultrasonic technology allows you to measure the thickness of metals, plastics, composites, and more, simply by placing the probe on the surface. The gauge sends high-frequency sound waves through the material, and by measuring how long the echo takes to return, it calculates the material’s thickness with incredible accuracy. The process is fast, efficient, and doesn’t compromise the integrity of the structure being tested.
But when exactly should you use an ultrasonic thickness gauge? Is it only for aging pipelines or corroded tanks, or does it have a place in routine inspections as well?
In this blog, we’ll explore when to use an NDT ultrasonic thickness gauge, the scenarios where it proves most valuable, and the advantages it offers across various industries. Whether you’re performing routine maintenance, checking for corrosion, or verifying weld integrity, this guide will help you understand how and when this precision tool can make a critical difference.
What is an NDT Ultrasonic Thickness Gauge?
An NDT (Non-Destructive Testing) Ultrasonic Thickness Gauge is a specialized instrument used to measure the thickness of a material without compromising its integrity. It works by emitting high-frequency sound waves through the material. . The ultrasonic method is non-invasive, making it ideal for situations where traditional measurement techniques might not be applicable.
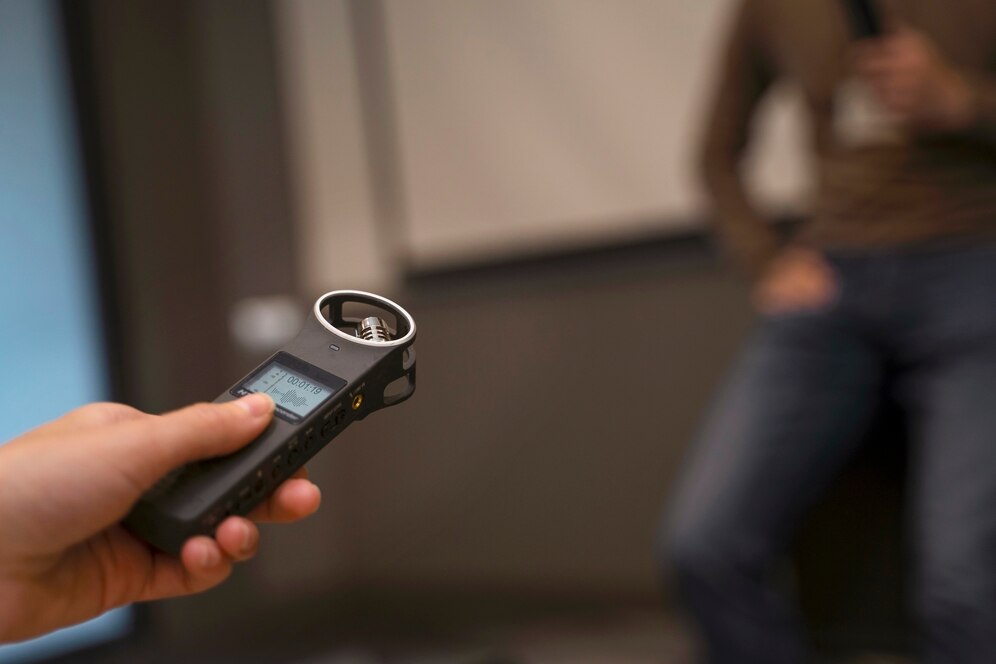
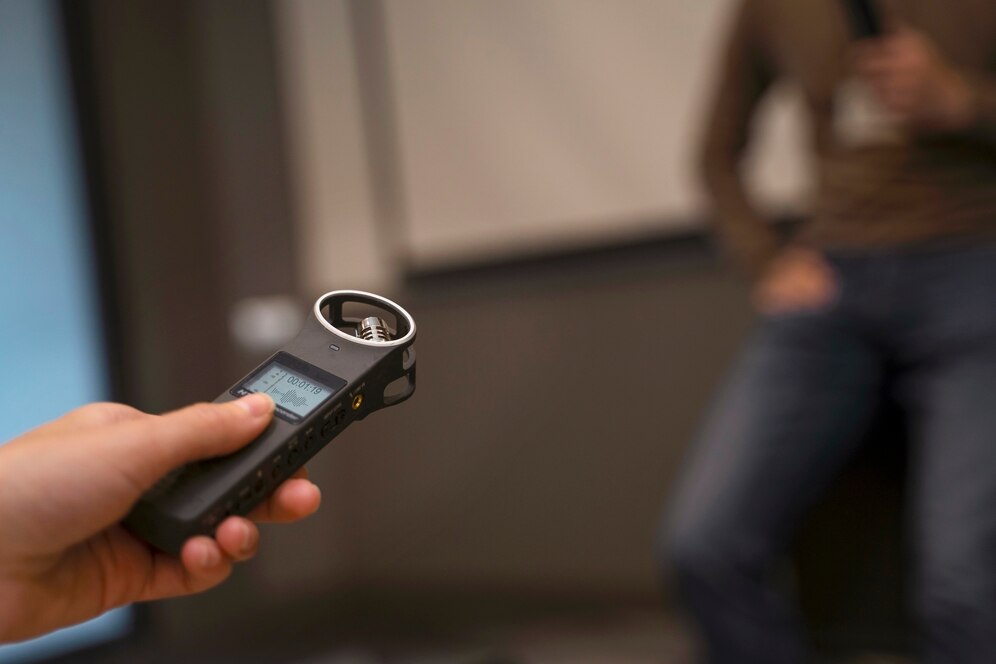
Key Applications of NDT Ultrasonic Thickness Gauges
Pipe and Pressure Vessel Inspection:
Ultrasonic thickness gauges are frequently used in industries that involve pipelines, pressure vessels, and boilers. These applications require periodic thickness measurements to check for wear, corrosion, or degradation of the material over time.Corrosion Monitoring:
Corrosion is a common issue in various industries, especially in marine, oil, and gas sectors. An ultrasonic thickness gauge helps detect thinning due to corrosion without having to dismantle or damage the equipment.Material Quality Control:
In manufacturing and construction, ultrasonic thickness gauges are used for quality control to ensure materials meet the required thickness specifications. This is crucial in industries where the strength and integrity of materials are critical.Welding Inspections:
Ultrasonic thickness gauges are useful for inspecting the quality of welds, helping to verify if the material thickness is consistent and meets the required standards.Maintenance of Structural Components:
Regular thickness measurements are vital in maintaining structural components like tanks, walls, and other load-bearing structures, ensuring that they remain safe and operational.
Benefits of Using an Ultrasonic Thickness Gauge
Non-Destructive:
The most significant benefit of using an ultrasonic thickness gauge is its non-destructive nature. It doesn’t damage the material or structure being measured, ensuring that you get accurate readings without compromising the integrity of the object.Precision and Accuracy:
Ultrasonic gauges provide highly accurate and reliable thickness measurements, which are crucial for industries that require strict adherence to safety standards and regulations.Wide Material Compatibility:
Ultrasonic thickness gauges work effectively on metals, plastics, composites, and even ceramics—making them a go-to solution across diverse industries from aerospace to automotive.Cost-Effective:
By preventing the need for disassembly or destruction of materials to measure their thickness, ultrasonic gauges save both time and money. It reduces downtime and helps companies avoid unnecessary replacement costs.Portability:
Many ultrasonic thickness gauges are portable and easy to handle, making them suitable for both on-site and in-lab inspections.
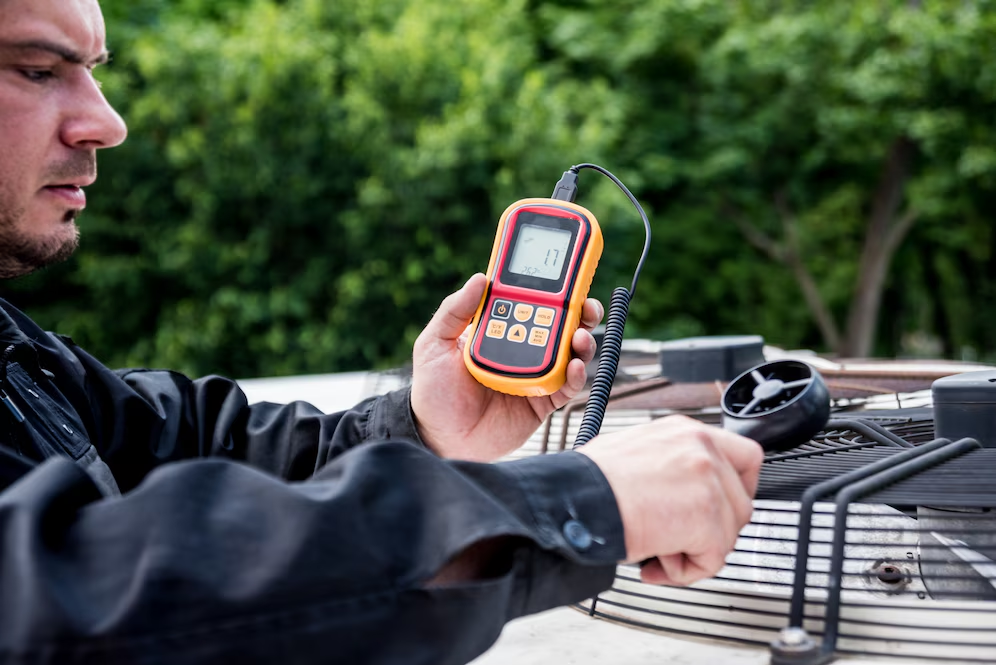
When to Use an Ultrasonic Thickness Gauge
Preventing Corrosion Damage:
If you’re managing assets exposed to harsh environmental conditions, such as pipes in a chemical plant or vessels in a marine environment, corrosion is a concern. Use an ultrasonic thickness gauge regularly to check for thinning of the material caused by corrosion, which could lead to leaks or failures if left unmonitored.Routine Inspections:
For any infrastructure or equipment subject to wear and tear, a routine inspection is key. Whether it’s the walls of a tank, the floor of a bridge, or pipelines, ultrasonic thickness gauges can be used as part of a routine inspection schedule to detect early signs of damage or wear.When Internal Access is Not Possible:
If you need to measure the thickness of a material that cannot be accessed internally or cannot be dismantled, ultrasonic thickness gauges are the ideal solution. Their ability to measure from the external surface of the material makes them highly useful in such situations.Monitoring Welds or Joints:
Ultrasonic thickness gauges are effective in checking the thickness of welded joints. They can ensure that the welds are strong, meet quality standards, and have the right thickness to prevent cracks or failures in the structure.Compliance with Industry Regulations:
Many industries have strict regulations when it comes to material integrity and safety standards. Using an ultrasonic thickness gauge helps ensure compliance with these regulations, helping avoid penalties and improve operational safety.
Conclusion
In industries where material integrity is critical, the NDT ultrasonic thickness gauge plays a crucial role in monitoring and maintaining equipment, structures, and infrastructure. Whether you’re dealing with routine inspections, corrosion monitoring, or ensuring compliance with industry standards, this tool provides reliable, accurate, and non-destructive measurements. Regular use of an ultrasonic thickness gauge can help prevent costly repairs, extend the lifespan of assets, and ensure the safety of operations.
If you’re looking for reliable ultrasonic thickness gauges and other precision tools, Acro Enterprise offers high-quality solutions tailored to your needs. Contact us today to learn more about how our tools can enhance your maintenance and inspection processes.
Need Expert Support to Take Your Business Further?
At Acro Enterprise, we specialize in helping businesses streamline operations and achieve sustainable growth through tailored solutions. Whether you’re just starting out or scaling up, our experts are here to guide you every step of the way.